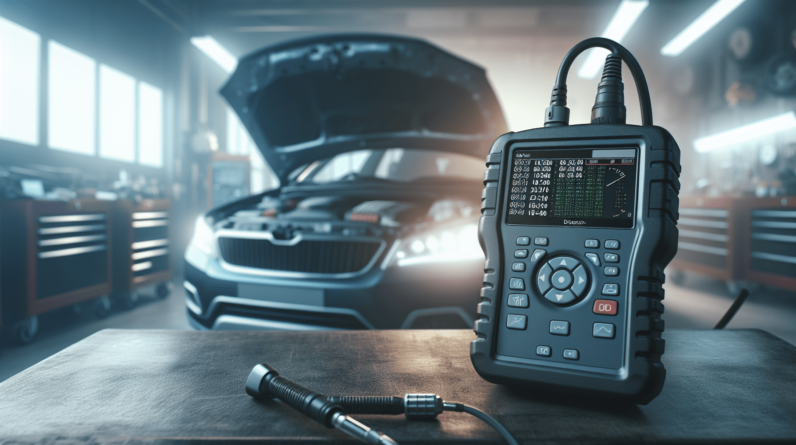
Have you ever wondered how much money you could save by regularly diagnosing and maintaining your equipment or vehicle? Regular diagnostics have increasingly become an essential aspect of asset management, leading to improved performance and minimized costs. They are not just beneficial but necessary for preventing costly repairs, extending the lifecycle of your equipment, and ensuring operational efficiency.
What Are Regular Diagnostics?
Regular diagnostics refer to the routine checking and analysis of equipment or vehicles to identify any anomalies that may lead to significant issues if left unaddressed. This process involves the use of specialized tools and techniques to assess various components, systems, and functions to ensure they operate as intended.
Importance of Regular Diagnostics
The primary objective of regular diagnostics is to have a proactive approach towards equipment management. Here’s why they are crucial:
- Early Detection of Problems: Identifying issues early on prevents them from turning into major, cost-intensive repairs.
- Extended Equipment Life: Regular maintenance ensures that machines and vehicles run smoothly, extending their lifespan significantly.
- Improved Efficiency: Well-maintained equipment operates more efficiently, reducing downtime and operational costs.
- Safety: Regular diagnostics can identify safety issues before they pose risks to personnel or property.
Types of Diagnostics
There are different types of diagnostics depending on the equipment or vehicle being assessed. Here are a few examples:
- Mechanical Diagnostics: Focuses on the physical components such as engines, belts, and gears.
- Electrical Diagnostics: Examines the electrical systems including wiring, batteries, and alternators.
- Software Diagnostics: For equipment that relies on software, this process checks for bugs, updates, and overall system integrity.
Benefits of Regular Diagnostics
Cost Savings
One of the most obvious benefits of regular diagnostics is the cost savings. By catching problems early, you avoid the exorbitant costs associated with major repairs or replacements.
Aspect | Without Diagnostics | With Regular Diagnostics |
---|---|---|
Repair Costs | High | Low |
Downtime | Extended | Minimal |
Lifespan Reduction | Significant | Moderate |
Operational Efficiency | Decreased | Increased |
Increased Reliability
When equipment undergoes regular diagnostics, it becomes more reliable. This reliability translates to less downtime and increased productivity. Imagine a factory machine breaking down in the middle of a crucial production run – the costs can be astronomical, not to mention the loss in customer confidence. Regular diagnostics ensure that such scenarios are minimized.
Safety Improvements
Safety is another critical benefit. Equipment and vehicles that are regularly diagnosed are less likely to fail unexpectedly, reducing the risk of accidents. This is particularly important in industries where heavy machinery is involved or where vehicle safety is paramount.
Improved Resale Value
Equipment or vehicles that have been regularly maintained often have higher resale values. Potential buyers are more inclined to invest in assets that have a well-documented maintenance history.
How to Implement Regular Diagnostics
Create a Maintenance Schedule
The first step in implementing regular diagnostics is to create a comprehensive maintenance schedule. This schedule should include the following:
- Frequency: How often the diagnostics will be performed, e.g., weekly, monthly, or annually.
- Tasks: Specific tasks that need to be performed during each diagnostic session.
- Responsible Personnel: Assignments of who will perform the diagnostics.
- Tools and Equipment Needed: Necessary tools and diagnostic equipment required for the tasks.
Train Your Team
It’s important that your team is well-trained in performing diagnostics. They should be familiar with using diagnostic tools and understanding the results. Consider regular training sessions to keep everyone updated on the latest techniques and technologies.
Keep Detailed Records
Maintaining detailed records of all diagnostic checks is essential. These records should include:
- Dates of diagnostics
- Issues identified
- Repairs executed
- Parts replaced
- Any monitoring or follow-up required
Use Diagnostic Tools
Investing in high-quality diagnostic tools can make a significant difference. These tools include various types of sensors, software programs, and mechanical diagnostic tools.
Third-Party Services
In some cases, your organization may not have the expertise or resources to perform diagnostics in-house. In such scenarios, hiring third-party diagnostic services can be beneficial. These professionals bring expertise and advanced tools to perform thorough diagnostics.
Case Studies
Manufacturing Industry: Preventing Machine Downtime
In the manufacturing sector, machine downtime can be hugely costly. A leading manufacturer implemented regular diagnostics on its assembly line machinery. Over one year, they saw a reduction in major repair costs by 50% and an increase in production efficiency by 20%.
Transportation Industry: Fleet Management
A bus company that regularly performed diagnostics on its fleet experienced fewer breakdowns and enhanced passenger safety. By using specialized diagnostic tools to check engine performance and other critical systems, they managed to cut maintenance costs by 30% annually.
Healthcare Industry: Medical Equipment Maintenance
Medical equipment is crucial and often life-saving. A hospital initiated a regular diagnostic program for its imaging machinery, lab equipment, and patient monitoring systems. The program helped identify potential failures early, preventing costly repairs and ensuring continuous, reliable service to patients.
Cost-Benefit Analysis
To truly understand the value of regular diagnostics, conducting a cost-benefit analysis is worthwhile. Here’s a simplified example:
Factor | Without Regular Diagnostics | With Regular Diagnostics |
---|---|---|
Annual Repair Costs | $50,000 | $20,000 |
Annual Maintenance Costs | $10,000 | $15,000 |
Downtime Costs | $30,000 | $5,000 |
Resale Value of Equipment (after 5 years) | $5,000 | $15,000 |
Total Cost Over 5 Years | $475,000 | $250,000 |
In this example, investing in regular diagnostics results in substantial savings over five years, totaling $225,000.
Key Challenges and Solutions
Initial Cost
One challenge is the initial cost of setting up a diagnostics program. It involves purchasing diagnostic tools, training staff, and possibly hiring third-party services. To mitigate this, consider the long-term savings and potential ROI. Additionally, starting with essential diagnostics and gradually expanding the program can help manage costs.
Technological Adaptation
Keeping up with evolving diagnostic technologies can be overwhelming. Regular training and partnerships with diagnostic tool providers can help keep your team updated.
Resistance to Change
Employees may resist new diagnostic routines. Effective communication about the benefits, coupled with proper training, can help alleviate resistance. Showing tangible results, like cost savings and reduced downtime, can further convince stakeholders of the program’s efficacy.
Future of Diagnostics
As technology advances, the realm of diagnostics is also evolving. Future trends include:
Machine Learning and AI
Machine learning and AI are set to revolutionize diagnostics. These technologies can predict failures before they happen, based on data trends and patterns, making diagnostics even more proactive and accurate.
Internet of Things (IoT)
IoT allows equipment to communicate and report issues in real-time. For instance, sensors on a vehicle can automatically send diagnostic data to a monitoring system, which can then alert the maintenance team of any issues.
Remote Diagnostics
Remote diagnostics allow specialists to assess equipment without needing to be physically present. This is beneficial for organizations with assets spread across different locations.
Conclusion
The advantages of regular diagnostics are clear and multifaceted. They not only save costs by preventing major repairs but also enhance reliability, safety, and the overall lifespan of equipment. Implementing a systematic diagnostics program involves planning, training, and investing in the right tools but the long-term benefits far outweigh these initial efforts.
By adhering to regular diagnostics, organizations can achieve remarkable operational efficiency, financial savings, and safety improvements. The potential for integrating advanced technologies like AI and IoT into diagnostics represents an exciting future that promises even more enhancements in asset management. Therefore, the question isn’t whether to adopt regular diagnostics, but rather, how soon and effectively can you implement them to start reaping the benefits.