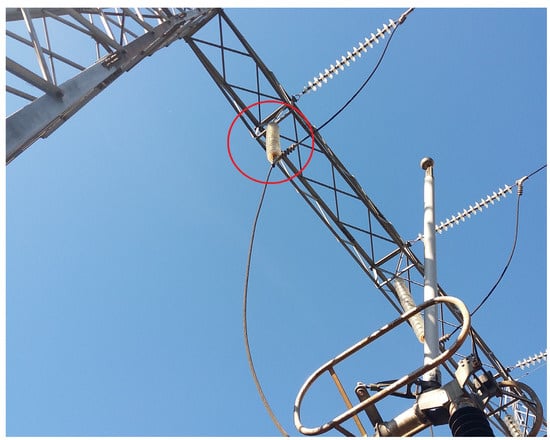
Have you ever wondered how complex electrical issues in modern systems are diagnosed and resolved? This article delves into a detailed case study that highlights the methodologies and technological advancements utilized in addressing intricate electrical problems. My objective here is not only to illustrate the problem-solving journey but also to underscore the importance of advanced diagnostics in contemporary electrical systems.
This image is property of media.springernature.com.
Understanding the Problem
The complexity of modern electrical systems presents unique challenges. These systems are integrated, multifaceted, and contain numerous interconnected components that can fail in unpredictable ways. This case study concerns a manufacturing facility experiencing intermittent power disruptions, resulting in substantial downtime and financial losses.
Background
The manufacturing facility in question is a major production hub employing thousands of machines and equipment. Each piece of equipment relies on a sophisticated electrical infrastructure to function optimally. Given the scale and complexity of operations, pinpointing the exact cause of electrical issues is akin to finding a needle in a haystack.
Initial Symptoms
The primary symptoms experienced included:
- Frequent power outages in certain sections of the facility
- Erratic machine performance
- Unexplained tripping of circuit breakers
These issues were sporadic, making it difficult to predict or easily trace the root cause. This erratic behavior made a robust diagnostic approach essential.
Diagnostic Approach
The importance of a systematic diagnostic approach cannot be overstated. It involves meticulous planning and the deployment of advanced diagnostic tools and methods to identify the root cause efficiently.
Step 1: Preliminary Inspection
A preliminary inspection was conducted to identify any obvious signs of wear, damage, or malfunction. This included:
- Visual Inspection: Checking for any visible signs of damage or wear in wiring, connections, and equipment.
- Thermal Scanning: Identifying any hotspots that might indicate excessive heat and potential failure points.
- Noise Analysis: Listening for any abnormal sounds from equipment that may indicate mechanical or electrical issues.
Step 2: Data Collection
Accurate data collection is critical for effective diagnostics. In this case, a series of advanced tools and technologies were utilized to gather relevant data:
Tool/Technique | Purpose |
---|---|
Power Quality Analyzer | Measure voltage, current, and power factor. Determine the overall power quality. |
Oscilloscope | Visualize waveforms and detect any irregularities in the electrical signals. |
Data Loggers | Continuously monitor power supply over an extended period. |
Thermal Imaging Camera | Detect overheating in electrical components and connections. |
Step 3: Analyzing Data
After gathering data, the next step was a thorough analysis:
- Power Quality Analysis: Power quality analyzers revealed significant voltage sags and swells that correlated with the power outages.
- Oscilloscope Findings: Oscilloscope waveforms showed transient spikes, indicating potential issues with load variations or faulty equipment.
- Thermal Imaging: Some circuits exhibited excessive heating, suggesting electrical resistance issues possibly due to poor connections or faulty components.
Identifying the Root Causes
With the data in hand, the focus shifted to identifying the underlying causes. The analysis revealed three primary issues contributing to the facility’s electrical problems:
Issue 1: Voltage Fluctuations
Voltage fluctuations were a significant factor. The power quality analysis indicated frequent voltage sags and swells, disrupting sensitive machinery. This was likely due to the high demand and load variations within the facility.
Issue 2: Transient Spikes
Transient spikes discovered through oscilloscopic analysis suggested erratic loads or faulty equipment affecting the power supply stability. Further investigation pointed to specific equipment that caused these spikes during their operation.
Issue 3: Overheating Circuits
Overheating in certain circuits was identified using thermal imaging. High resistance due to poor connections or aging components was resulting in excessive heat generation, leading to tripped circuit breakers and potential fire hazards.
Solution Implementation
Having identified the root causes, the next phase involved implementing solutions to rectify these issues comprehensively.
Resolving Voltage Fluctuations
To mitigate voltage fluctuations, the following steps were taken:
- Installation of Voltage Regulators: Voltage regulators were installed to ensure stable voltage supply by compensating for sags and swells.
- Upgrade of Electrical Infrastructure: The facility’s electrical infrastructure was upgraded to handle high demand and load variations more efficiently.
- Load Balancing: Equipment loads were redistributed to balance demand and reduce fluctuations.
Managing Transient Spikes
For the transient spikes, the following measures were implemented:
- Surge Protectors: Installation of surge protectors to safeguard against transient spikes.
- Equipment Maintenance: Regular maintenance schedules were established for equipment causing erratic loads to preclude spikes.
- Isolation Transformers: Introduction of isolation transformers for sensitive equipment to prevent spikes from affecting the overall system.
Addressing Overheating Circuits
To address the overheating circuits:
- Rewiring and Connection Tightening: All poor connections were identified and rectified, rewiring sections where necessary and tightening loose connections.
- Component Replacement: Aging components causing high resistance were replaced.
- Improved Ventilation: Cooling systems were enhanced to ensure proper ventilation and reduce heat accumulation in circuit areas.
This image is property of www.mdpi.com.
Outcome and Impact
The implemented solutions yielded positive results and marked improvements in the manufacturing facility’s electrical stability and operational efficiency.
Measurable Improvements
Metric | Before Solution | After Solution |
---|---|---|
Power Outages | Frequent | Rare |
Circuit Breaker Trips | High | Low |
Equipment Performance | Erratic | Stable |
Financial Impact
Reduced downtime translated to significant financial savings. The facility experienced a substantial reduction in losses associated with production halts and equipment malfunction.
Long-term Benefits
The long-term benefits of these interventions included increased operational reliability, extended equipment life, enhanced safety, and fewer maintenance requirements.
Lessons Learned
The case study highlighted several key lessons integral to managing complex electrical issues effectively:
Importance of Advanced Diagnostics
The role of advanced diagnostics in identifying and addressing root causes cannot be overstated. Tools such as power quality analyzers, oscilloscopes, and thermal imaging cameras are pivotal in detailed and accurate diagnostics.
Holistic Approach
A holistic approach to problem-solving, considering not only immediate fixes but also long-term solutions, is crucial. Ensuring stable power supply, regular equipment maintenance, and proper cooling mechanisms are integral to preventing recurrent issues.
Proactive Maintenance
Proactive maintenance schedules help in early identification of potential problems before they escalate. Regular inspections and timely interventions are essential to sustaining an efficient electrical system.
Continuous Monitoring
Continuous monitoring using data loggers and similar tools enables ongoing observation of the electrical system, helping in early detection of anomalies and quick resolution of issues.
This image is property of media.springernature.com.
Conclusion
In conclusion, the effective resolution of complex electrical issues in modern systems requires a methodical and advanced diagnostic approach. This case study demonstrates how leveraging state-of-the-art diagnostic tools and meticulous planning can identify root causes and implement effective solutions. By adopting such comprehensive strategies, facilities can significantly enhance their operational efficiency, safety, and financial performance. The lessons learned are not only applicable to manufacturing facilities but across various sectors where electrical stability and reliability are paramount.